Risk Based Inspection (RBI)
Risk-Based Inspection (RBI) methodology helps companies to clearly identify, assess, map and mitigate any risks which can compromise equipment integrity. RBI is an evergreen process and it’s a journey from uncertainty to certainty about the risks, to know the risks and to quantify them.
The methodology focuses on addressing risks that can be controlled through proper mitigations, monitored through proper inspections and quantified through proper analysis. During an implementation, engineers design inspection strategies (what, when, how to inspect) that most efficiently match forecasted or observed degradation mechanisms.
DroobTech delivers real value to the distinguished clients by protecting their brand and reputation and by ensuring the safe and efficient operation of their products, equipment and plant assets. We help our clients to save time and money by avoiding the costs and loss of revenue due to product, equipment and asset defects or failures, all studies are done with the minimum of disruption to production processes and schedules.
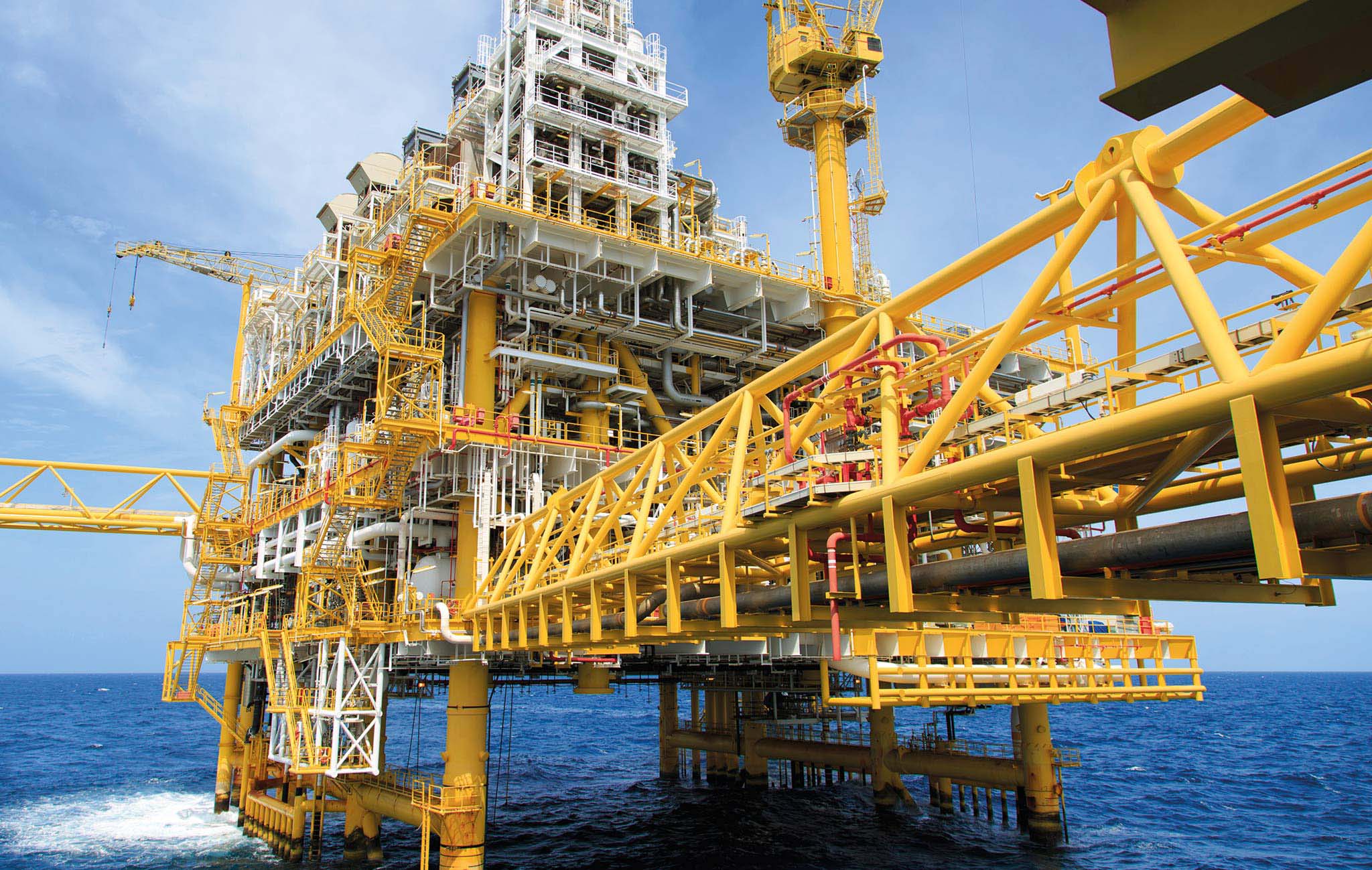
Risk-Based Inspection (RBI)
Fully integrated enterprise asset management solution in the industry is useful for avoiding or minimizing unplanned shutdowns for oil and chemical plants.
We have a wide range of expertise and resources including the software to serve the industry for Risk Based Inspection and Maintenance ventures. Our local and international experts, have served and met the industry needs to execute the various RBI Projects. RBI is carried as per guidelines mentioned in API 580 and 581 methodologies; also, we can extend our services based on other local and international standard practices.
Our risk-based inspection services include (and are not limited to):
- Assessment of process operations that will impact your production, operation, material integrity and degradation rates Determination of the remaining lifetime of assets
- Gap analysis
- Identification of operational risks, using recognized industry standards
- Identification of the appropriate inspection intervals
- Development of plant inspection plans
- Review of technical specifications and construction materials
- Specification of risk ranking level and determination of the respective risk acceptance level
- Specification of the necessary inspection and maintenance tasks
- Development of On Stream Inspection (OSI) Diagrams and Programs
- Condition Monitoring Locations (CML/TML) development and Optimization for existing CML Programs
- Small Bore (SB) Integrity Programs development
- Steam Traps Integrity Programs development
- Pipe Supports Integrity Programs development
- Management programs for Corrosion Under Insulation (CUI)
- Management Programs for Corrosion Under Pipe Support
- Development of Integrity Operating Windows (IOW) Programs
- Condition Monitoring Locations (CML/TML) development and Optimization for existing CML Programs
- Small Bore (SB) Integrity Programs development
- Steam Traps Integrity Programs development
- Pipe Supports Integrity Programs development
- Management programs for Corrosion Under Insulation (CUI)
- Management Programs for Corrosion Under Pipe Support
- Development of Integrity Operating Windows (IOW) Programs